Per poter stampare efficaciememte è necessario riconoscere i vari problemi che si incontrano in un processo di stampa. In questa lezione cercheremo di trattare le problematiche più comuni nella Stampa 3D, le cause e le soluzioni per ognuno di essi.
Adesione al piano di stampa
Abbiamo già accennato a questo tipo di problema nel capitolo precedente parlando di come trovare la giusta distanza tra ugello e letto di stampa, tuttavia si possono presentare problemi anche nel caso avessimo calibrato al meglio la stampante per ciò che concerne questo aspetto. In particolare, durante la stampa, il pezzo che era inizialmente saldamente assicurato alla piattaforma potrebbe staccarsi. Le cause possono essere diverse, tra esse: un piatto di stampa non perfettamente uniforme, un urto tra il pezzo e la testina di stampa o movimenti troppo bruschi della stampante.
Per risolvere questo problema possiamo agire in diversi modi.
- Utilizzare collanti o adesivi: per aumentare l’adesione possiamo utilizzare i collanti richiamati nella quarta lezione, questo è il metodo più efficace.
- Diminuire la velocità di stampa: un’estrusione troppo veloce può provocare disomogeneità nel filamento, diminuendola otterremo uniformità oltre che un ottimo primo layer.
- Piattaforme di adesione: all'interno dello slicer abbiamo la possibilità di creare supporti aggiuntivi chiamati Brim e Raft atti ad aumentare il vuoto creato tra il pezzo e il letto di stampa, aumentando l’adesione. Parleremo approfonditamente di queste opzioni in un articolo futuro.
Warping
Con questo termine facciamo riferimento alle curvature che possono crearsi agli angoli della stampa. Questo fenomeno è più presente nel caso di stampe di grandi dimensioni o nel caso si stiano utilizzando materiali con alta dilatazione termica come l’ABS.
Alcune soluzioni sono simili a quelle precedenti (come utilizzare collanti o utilizzare piattaforme di adesione) altre invece possono essere quelle elencate a seguire.
- Utilizzare un letto riscaldato: mantenere caldi i primi layer permette di terminare la stampa e non avere deformazioni.
- Stampare in un ambiente caldo: per fare ciò basterebbe racchiudere la stampante in un box, contenitore o enclosure di vario tipo per mantenere una temperatura ambientale sostenuta senza disperderla, causata dalla stampante stessa.
- Diminuire la velocità della ventola: a volte è possibile che il getto d’aria generato sia troppo potente, facendo raffreddare troppo in fretta il pezzo. Abbassando la velocità della ventola (in casi estremi, spegnendola del tutto) risolveremo questo problema.
Sotto-estrusione e sovra-estrusione
Per sotto-estrusione si intende l’estrusione di una quantità inferiore di materiale rispetto a quanto auspicato. Ciò può causare buchi, errori e scarsa resistenza meccanica nel pezzo finale. La sovra-estrusione, invece, è il problema contrario, si verifica quando l'ugello espelle più materiale del necessario, generando errori nelle misure finali del pezzo, cosa che potrebbe comportare collisioni durante il funzionamento.
Questi sono problemi molto comuni poiché possono dipendere dalle impostazioni dello slicer, dal tipo di filamento che stiamo utilizzando o dalla stampante stessa. Non sono difficili da riconosce poiché si noteranno evidenti errori sulla superficie della stampa. I vari layer, inoltre, e il percorso della testina saranno facilmente identificabili.
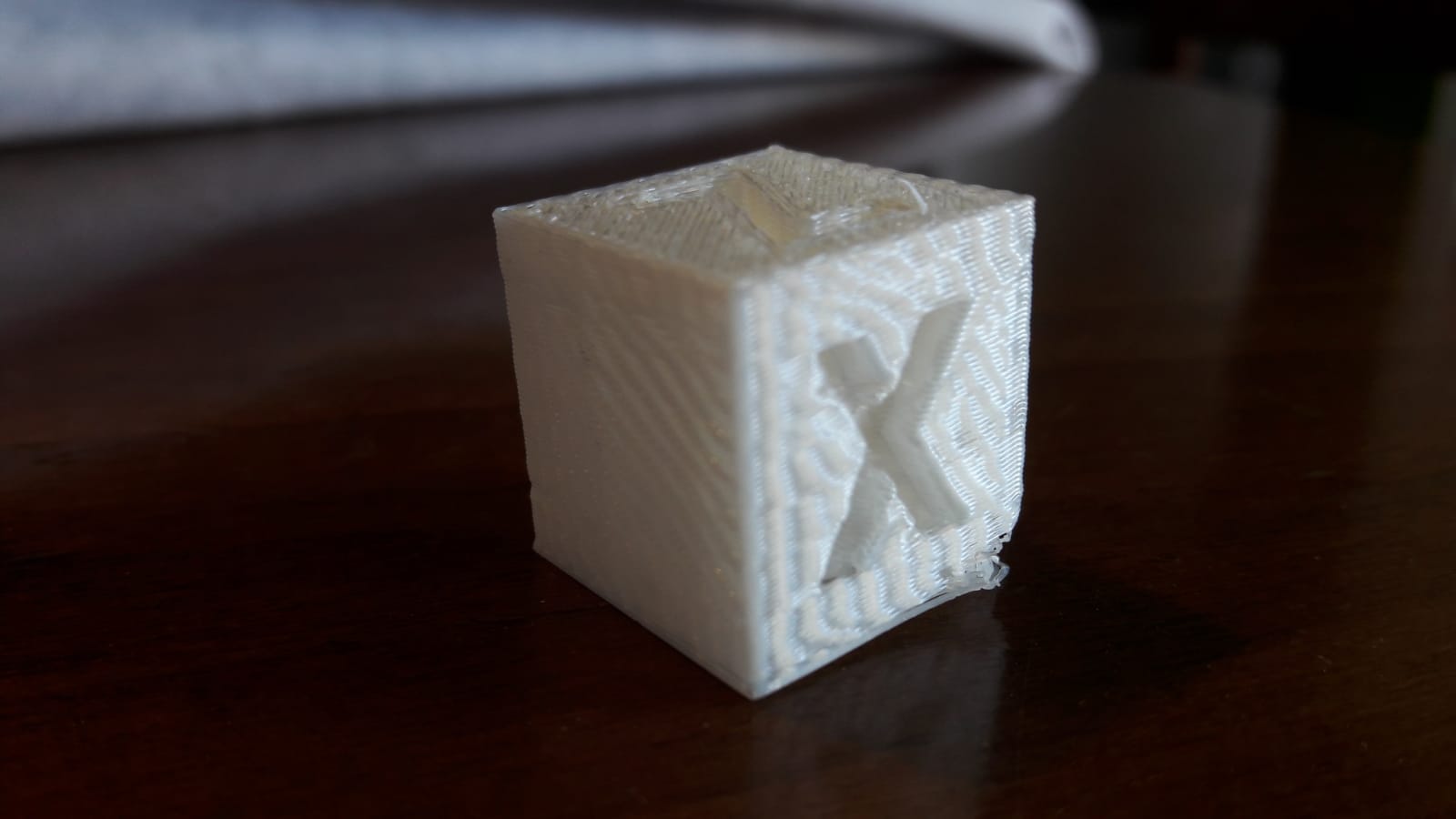
Esempio di sotto-estrusione
Per risolvere questi problemi possiamo agire neri come riportato qui sotto.
- Correggere il diametro del filamento utilizzato: a volte è possibile che la causa di tutto sia un parametro sbagliato nello slicer. Se il diametro del materiale che stiamo utilizzando non corrisponde con il valore impostato dovremo solo correggerlo.
- Regolare il moltiplicatore d’estrusione: all'interno di ogni slicer esiste un’opzione che permette di aumentare o diminuire la quantità di materiale estruso in percentuale. Nel caso in cui volessimo regolare con precisione l’estrusione questo è il parametro cui dovremo riferirci. (Es: Se volessimo aumentare di poco il materiale estruso ci basterà cambiare il valore da 100% a 105%, nel caso di sotto-estrusione. Per la sovra-estrusione agiremo in modo inverso portando il valore da 100% a 95%)
- Pulire l’hotend: se le soluzioni precedenti non dovessero funzionare allora è possibile che ci sia un blocco interno parziale che non consente la corretta estrusione del materiale. Pulendo meticolosamente i pezzi della stampante (o in casi estremi, sostituendoli) dovremmo risolvere il problema.
Disallineamento dei layer
Le stampanti 3D, come tutte le macchine CNC, non possono sapere se ci sono stati degli slittamenti o degli urti durante il loro processo (a meno che non sia presente una feature creata appositamente), per cui è possibile che, a causa di problemi esterni, la testina di stampa si sposti dalla posizione in cui dovrebbe trovarsi causando un disallineamento dei layer, stampando letteralmente un pezzo spezzato.
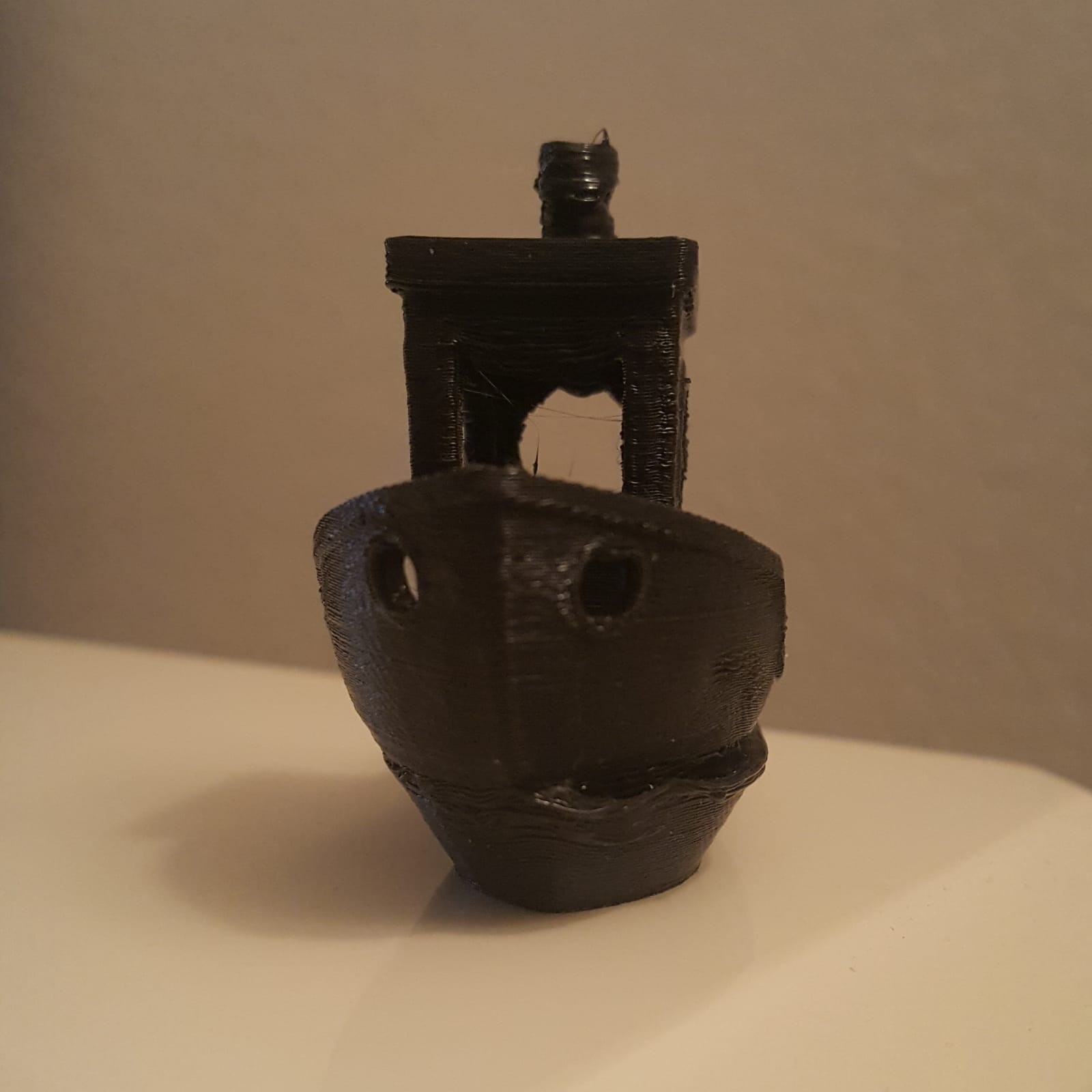
Disallineamento dei layer visibile nella parte inferiore della barca
Nel caso in cui la causa fosse stata esterna e sappiamo che non si ripeterà, ci basterà far ricominciare il processo da capo. Se il problema dovesse ripetersi la causa potrebbe essere ascritta alla stampante.
Ora illustreremo come comportarsi qualora si riscontri questa problematicità.
- Controllare i componenti strutturali della stampante: molte volte la causa potrebbero essere le viti troppo strette o troppo lente, condizione che comporta un movimento non uniforme dell’estrusore, oppure da veri e propri pezzi deformati (come ad esempio le guide), ciò causerebbe attrito fra i vari pezzi in movimento.
- Diminuire la velocità della testina di stampa: utilizzando velocità troppo elevate il momento generato dalla testina, quando cambia direzione, potrebbe sfasare la sua posizione.
Parti sottili che non vengono stampate
Questo è un caso un po’ particolare, dato che si manifesta solo stampando parti molto piccole o sottili. Le stampanti possiedono dei limiti fisici dovuti ai componenti con cui sono costruite, in questo caso ci riferiamo all'ugello poiché ha una misura precisa da cui deriva la qualità dei dettagli che queste sono in grado di creare. La stampa sarà dunque limitata alla dimensione del foro di uscita del materiale.
Per fare un esempio, se il foro dell'ugello avesse una misura di 0,4 mm, parti della stampa inferiori a questa misura non potranno essere stampate. Questo problema è già evidenziato nell'anteprima di stampa dello slicer, che non le visualizza.
Per aggirare l'ostacolo si può operare come leggerete nel prossimo elenco.
- Sostituendo l’ugello di stampa: banalmente, utilizzando un ugello con misura più piccola, potremo ottenere dettagli maggiori.
- Abilitando la stampa di parti sottili: all'interno dello slicer troveremo un’opzione che permette la stampa di perimetri sottili. Il risultato varia da stampante a stampante.
- Riprogettare il modello: nel caso fosse possibile, ridisegnare il pezzo con le misure supportate è sempre l’opzione migliore.
Anticipazioni
Nel prossimo articolo affronteremo altre situazioni complesse in cui potremmo incappare durante la Stampa 3d per essere preparati a ogni problema possa presentarsi.